Design Starts with Location: Protecting IMP Panels from the Ground Up
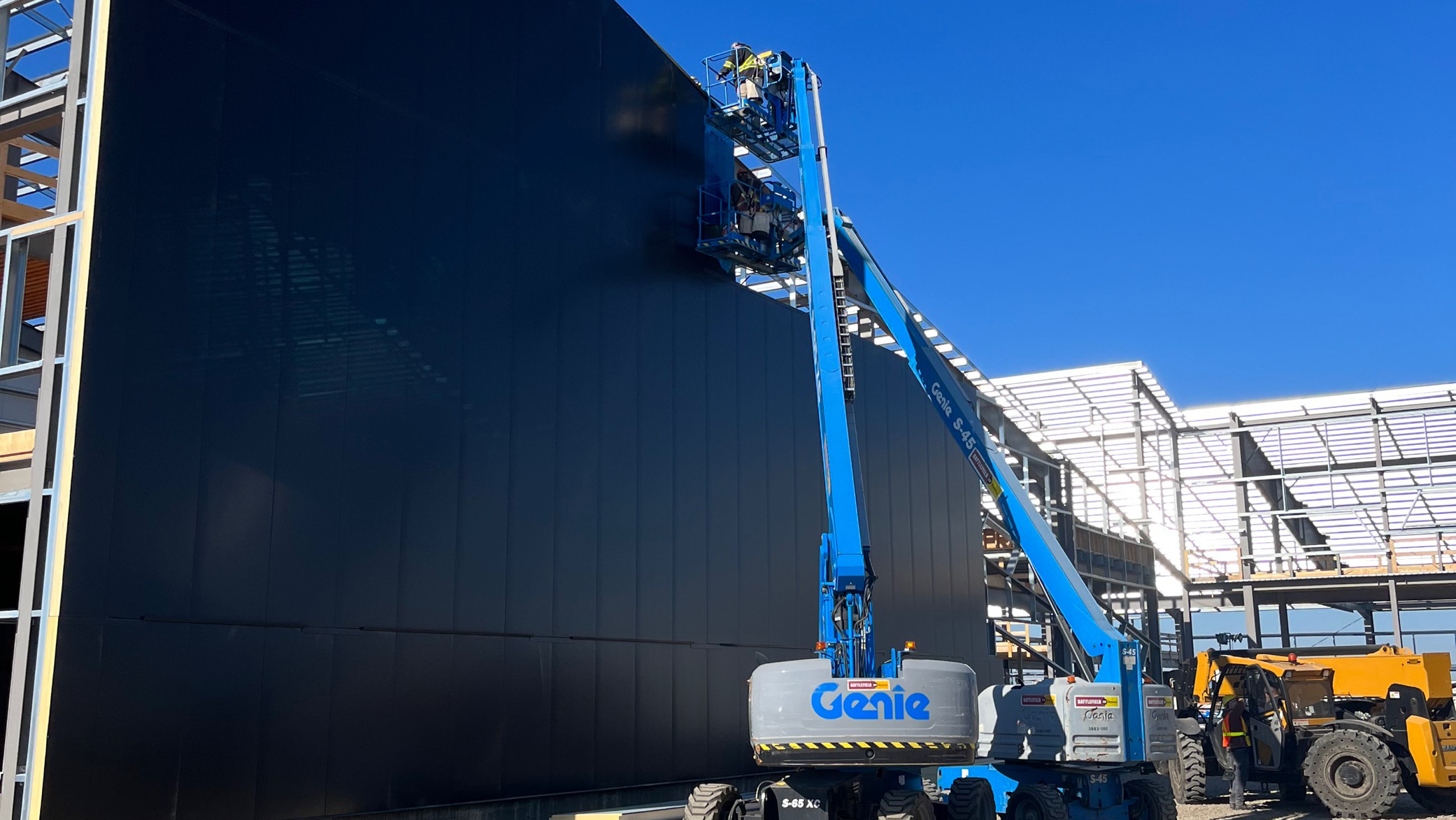
In my previous article I talked about a key component for a successful IMP installation being the proper placement and location of sealants to ensure a weathertight installation.
For this article, it is all about location, location – and everything around it. Designing and detailing IMP on your project must take product limitations into consideration for location and placement. The product has a durable interior and exterior steel face, but still has its limitations for impact damage from vehicles, forklifts and other occurrences. Minor scrapes, scratches and dents can be repaired without removing the panels, but some damage might require full panel replacement. IMP wall panels are installed using hidden clips within the joint. This configuration makes removing and replacing full wall panels arduous, time consuming and expensive.
Knowing this; the building, lot layout, end use, type of client, and traffic must be carefully looked at. This will ensure the location of IMP in critical areas is planned out at the design phase with long term durability in mind.
Thought must go into the traffic lanes around a building but also inside, to prevent damage from heavy impacts. This can be accomplished by using a lower course of CMU (concrete masonry unit) blocks, stonework or poured concrete on the bottom half of the walls in these high traffic areas and entrance lanes.
This should also include bollards at corners, entrance ways and critical path areas, both inside and out. Heavy steel exterior railing systems at dock level, along with overhead door sealers and bumper protection will take the impact from a truck trailer or forklift better than your IMP walls.
One area often overlooked, is the side or front of the building with grass for landscaping. These areas should be designed knowing an outside company could be taking care of lawn maintenance. Landscape features should be designed to keep lawn mowers and trimers away from the painted exterior finish. This can include rocks, shrubs or flower garden features. Trees can be used as well but must account for future growth, including the possibility that branches could scrape the painted finish overtime as the wind blows against the trees. I have seen patterns created in the finish by tree branches moving back and forth that have not be trimmed back.
Taking a few moments to review the plans and put thought into preventive maintenance can go a long way in keeping building owners happy by protecting the walls inside and out.
Remember – It’s not just the location of the IMP, it’s everything else around it.
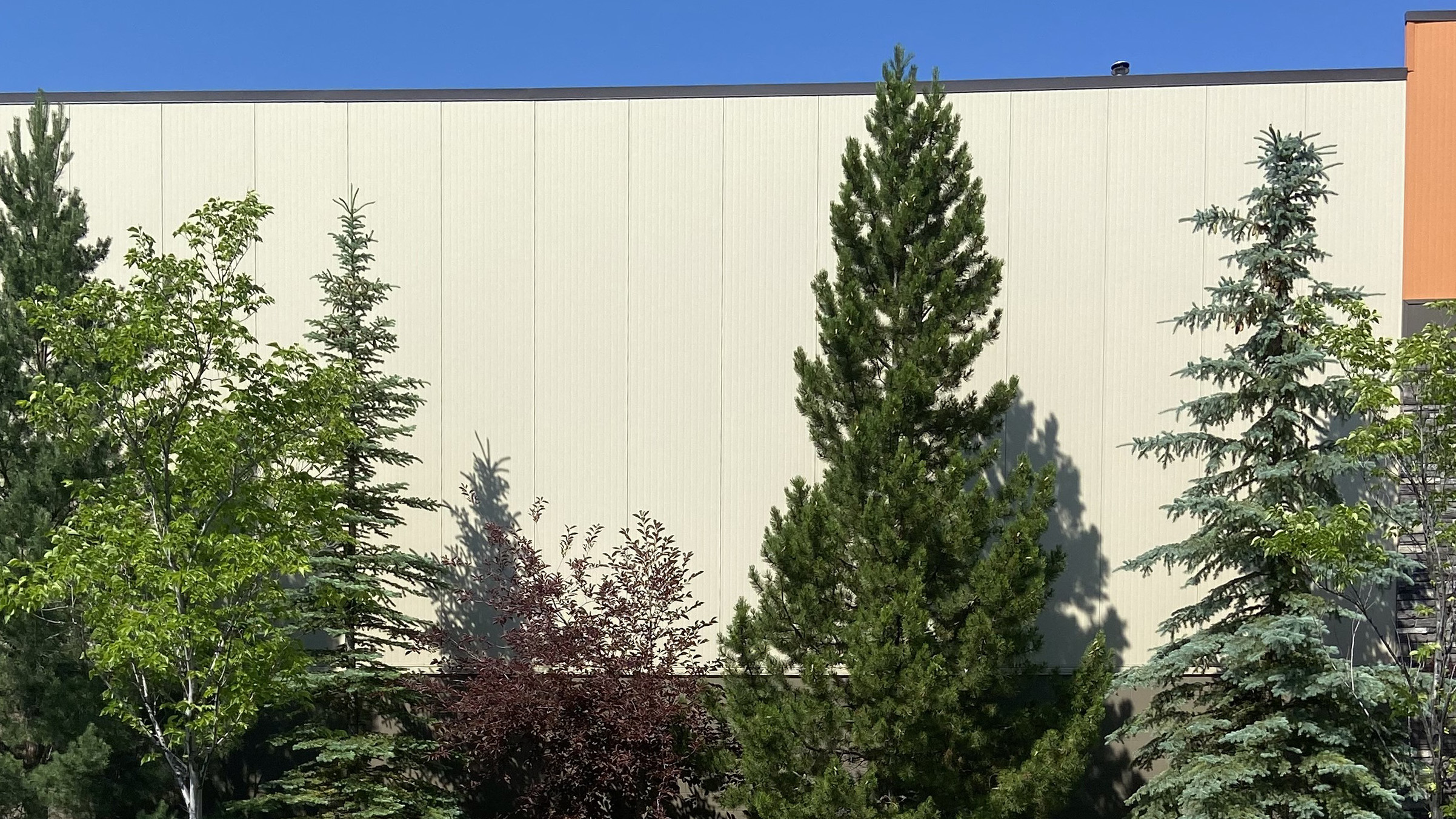
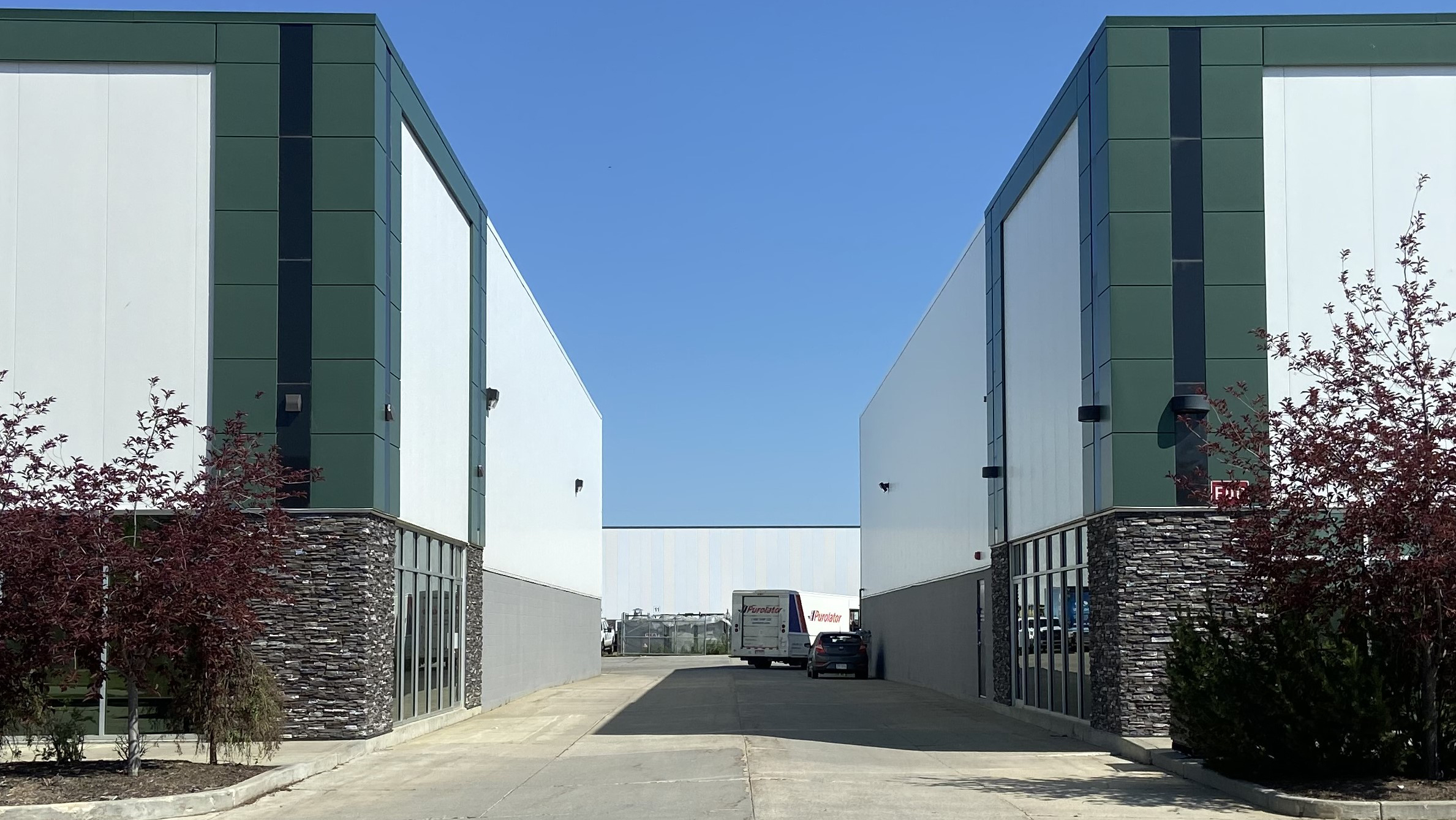
Written by:
David Forsey
Architectural Representative
BEHLEN Industries LP